CONNECTED IT – DATA INTELLIGENCE
Whether in warehouse management, factory construction or customer communication, the INDUS portfolio companies can network their processes in the right digital environment.
The manufacturing SME industry is of course very well aware of the potential of digitalization in the value chain: Faster. More efficient. Higher quality and better performance. The progress that companies can make is huge, and digital and automated processes often also optimize interfaces – both externally and internally.
GAINING DIGITAL EXPERTISE ...
That the INDUS companies are already working intensely to take advantage of this potential goes without saying. They are receiving strategic support from the holding company as well as specific project management from a team of specialists. One central aspect of the PARKOUR initiative “Improving Performance” is optimizing the value-adding core processes and improving operational excellence further. Good IT solutions are of course indispensable.
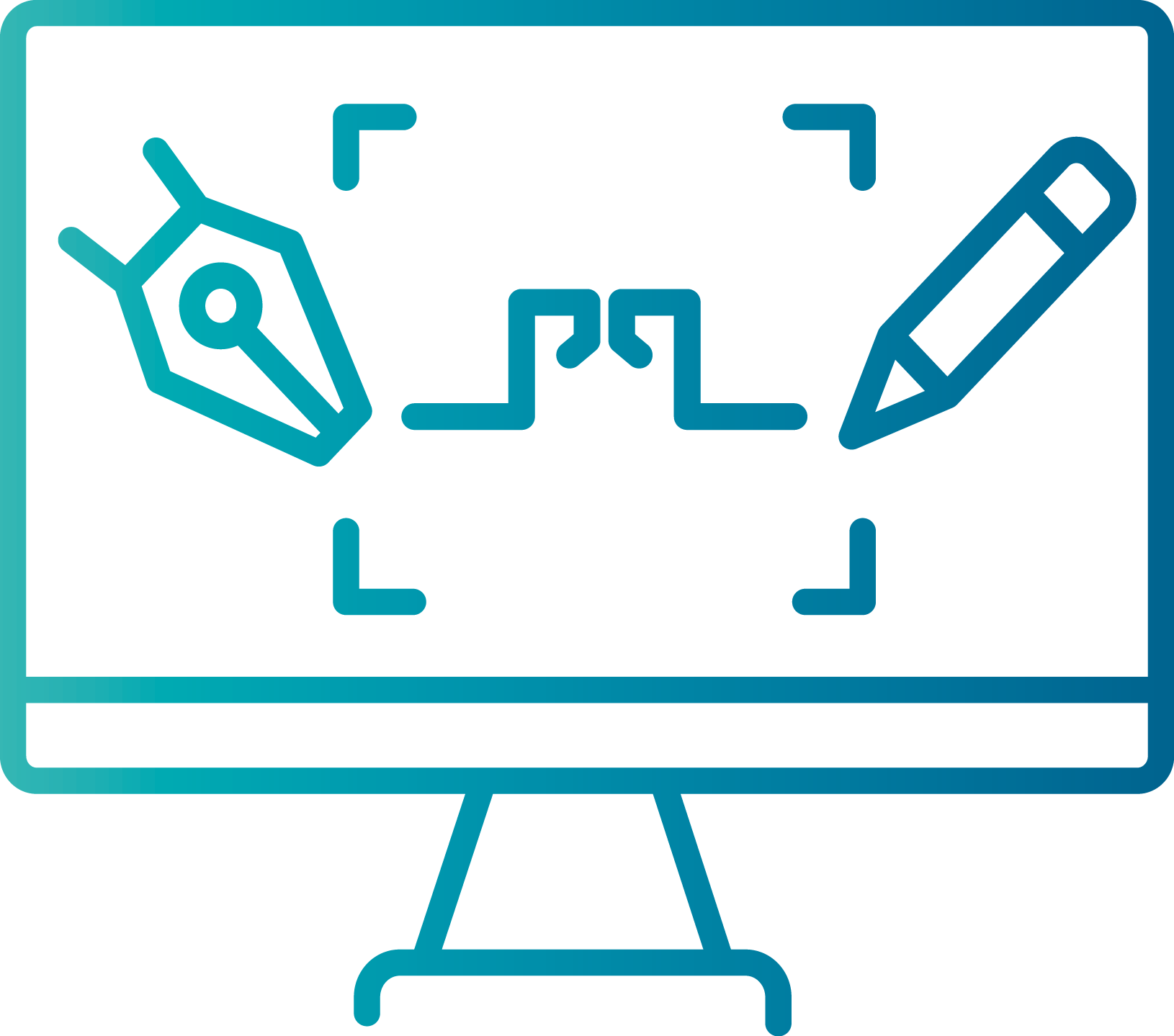
In 2023 alone, experts from the holding company provided support to a total of ten IT-related projects – from the selection processes and contract negotiations to implementation and optimization projects. The expert team’s role is that of sparring partner and knowledge multiplier. It also plays the role of messenger, sharing project experience within the Group so that the companies can learn from each other.
INDUS uses its network of external experts to boost the portfolio companies’ ability to develop digitally. An example of this is the “Project Manager Business Software” certificate course organized in collaboration with RWTH Aachen. Graduates of this course understand how to successfully launch business software and avoid typical pitfalls.
... AND USING IT
INDUS provides in-depth support, but the digital potential has to be recognized by the portfolio companies themselves. This also applies to IT systems, where a Group-wide approach may seem particularly tempting. But precisely here, individual solutions are the answer. Each INDUS portfolio company must find its own way to develop digitally – one in sales, one in production and another in logistics.
THREE EXAMPLES
The MIGUA measuring app: Precise communication in real time with MIGUPLAN
The INDUS portfolio company MIGUA is a specialist in the construction, manufacture and installation of joint profile systems. Visit an airport, railway station or shopping center, and you’re likely to encounter one of MIGUA’s approx. 600 joint profiles, channel systems or expansion joint tapes. And each of these products is individually made.
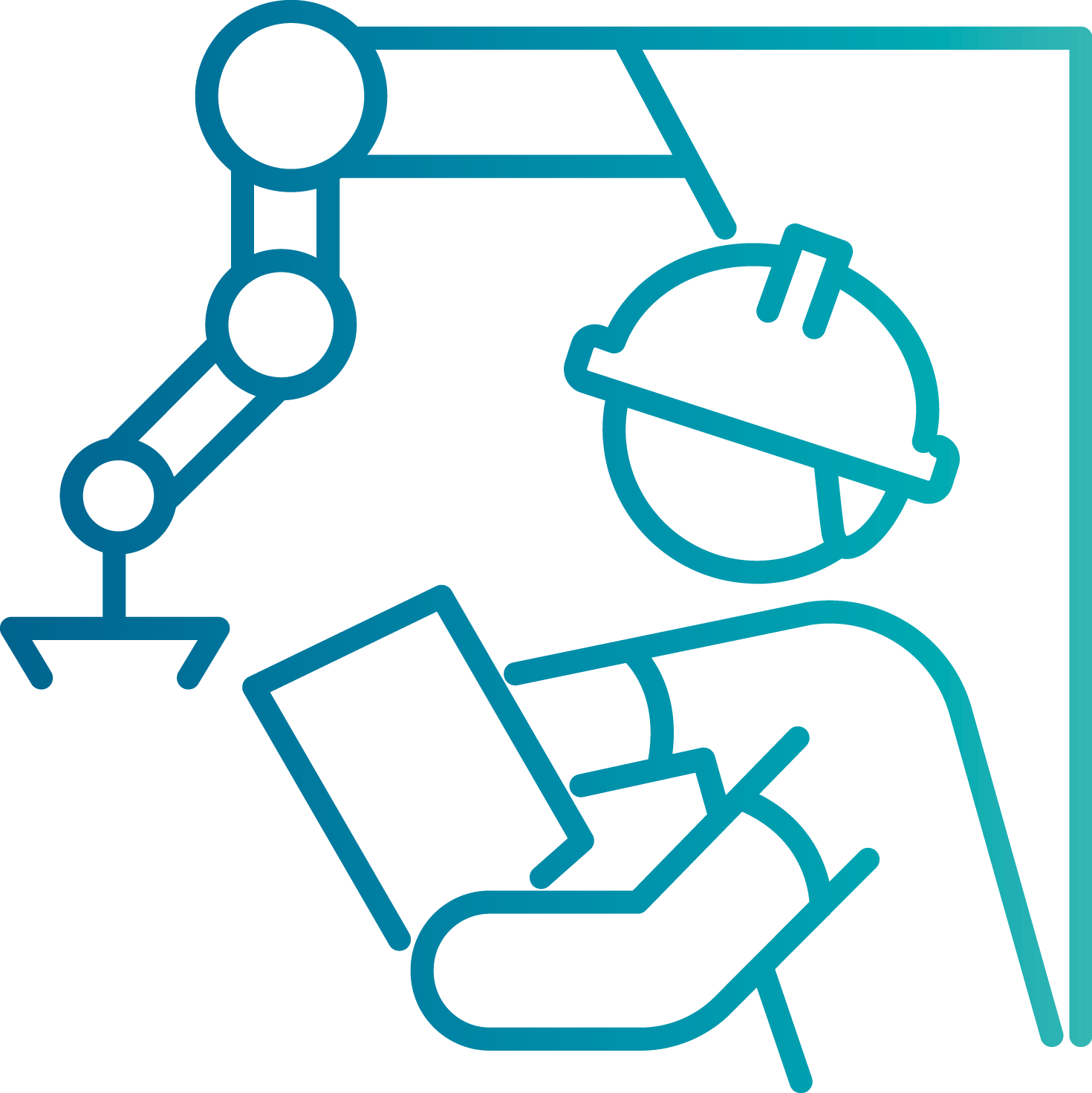
To make this possible, the sales team must accurately capture the customer’s requirements, which are often very unique, and communicate these for the next steps in the process. A “digital drawing board” is the key: MIGUPLAN, the measuring app developed by MIGUA, connects the field sales representatives virtually with both their company and the customers. The data, which comes from millimeter-precise measurements taken on site, is entered into the app directly by the field sales representatives and used to create drafts and quantity lists before being passed on to the customers and the experts in the service center. As soon as the sales representatives get the go ahead from the customer for the production drawings created in the app, the baton is passed to their colleagues, who then initiate the internal order and production process. The advantages are clear: Making the process digital avoids the time-intensive back and forth between sales and production, offers access to all project data at any time and place, and enables precise and reliable production.
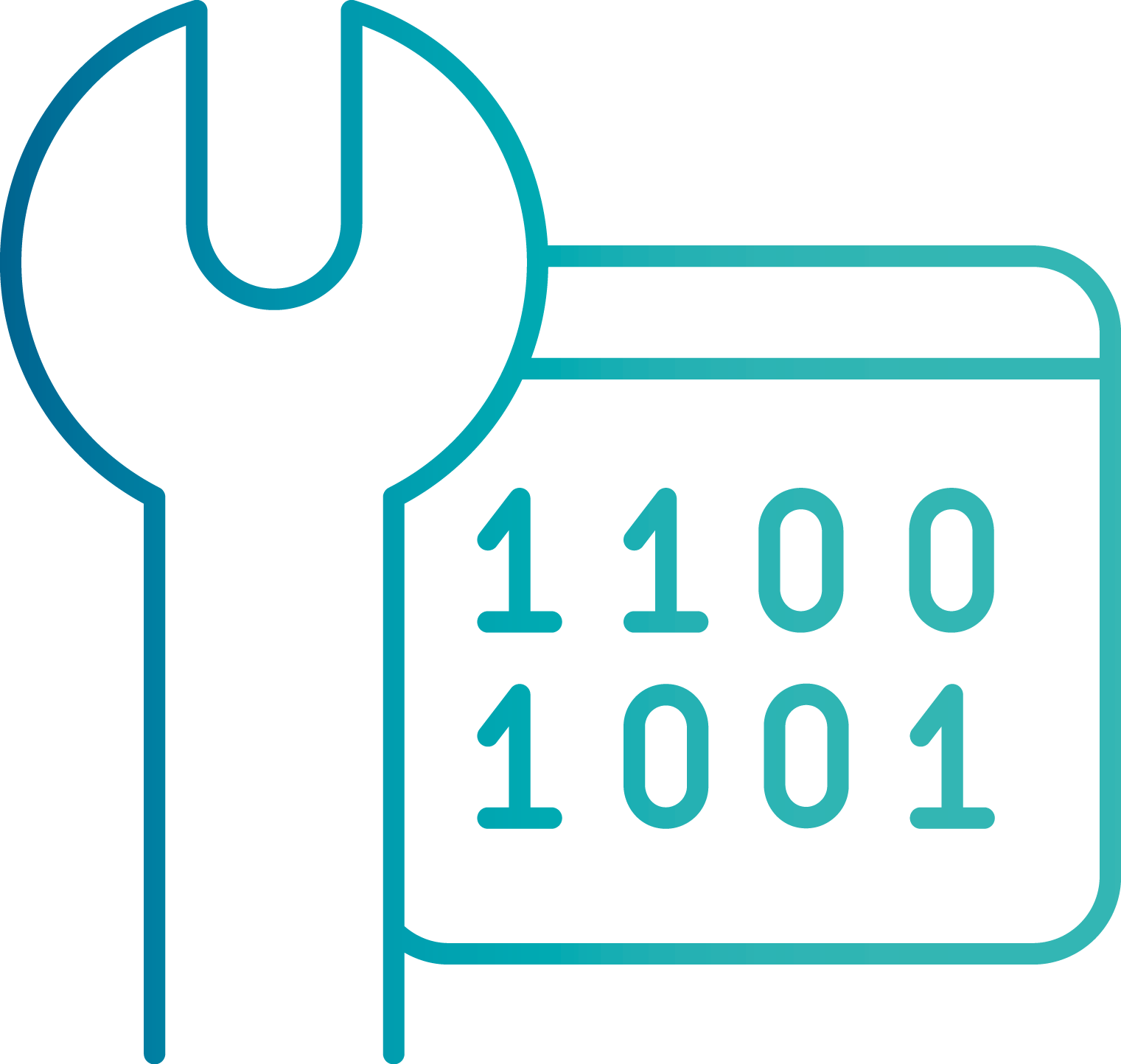
Machinery connection at BETEK
With around 400 employees, BETEK, located in Aichhalden, Baden-Württemberg, manufactures carbide-tipped wear parts and tool systems for road construction, civil engineering and agriculture, for example. With their investment in a new production facility, the company also took the opportunity to reconsider their concept for managing the extensive machinery.
Detail planning was optimized further with the introduction of a machine execution system (MES) – a key project for digitalization in the company. Basically, the MES, which has been tailored to the company’s needs, enables digital networking in production. The live connection of the individual machines to the ERP system allows the entire production process to be comprehensively planned, managed, monitored, traced and documented. What is the status of the machinery? What maintenance is due? Which construction contracts can be scheduled next? Many questions can be answered in real time at the press of a button with this new system.
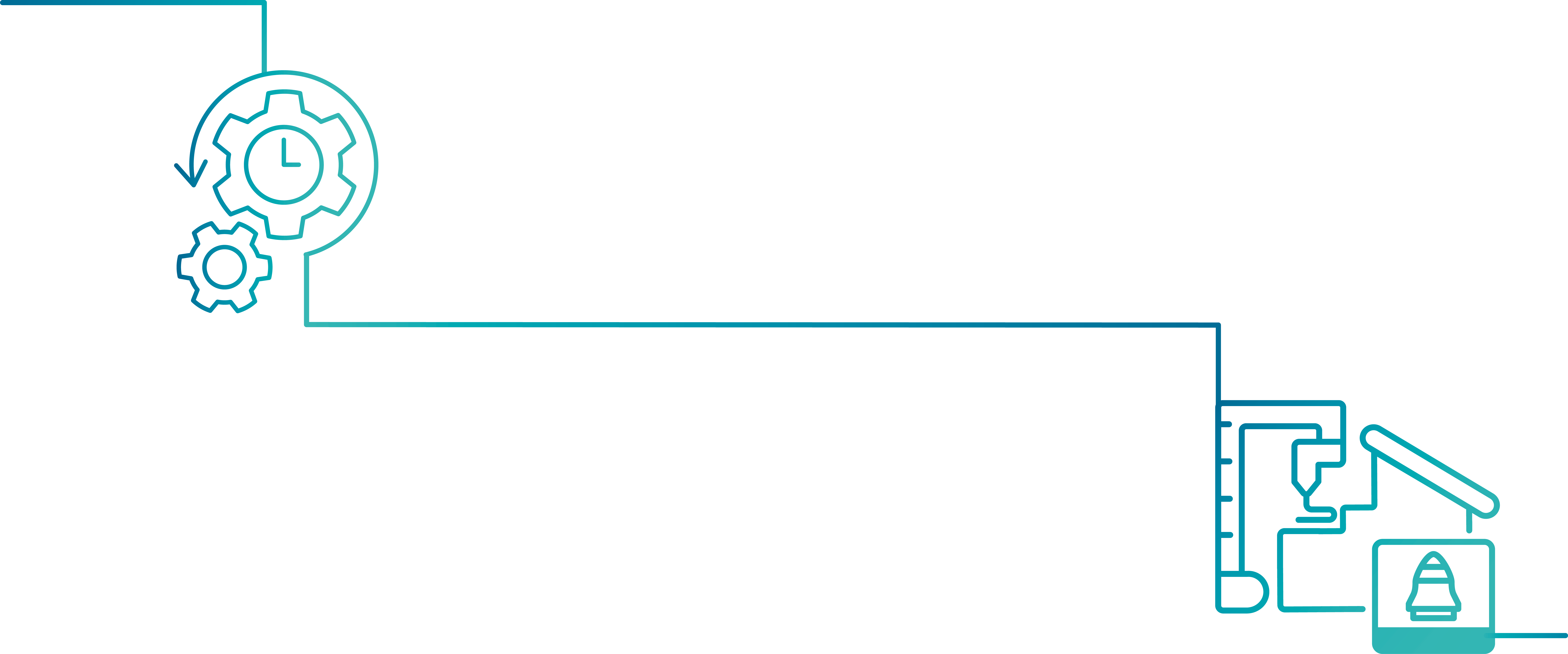
Smooth processes with MES:
- Secure capacity and production planning
- Recording operating data, determining lead times in real time (planned/actual)
- Down time/disruption recording
- Preventative maintenance
- User administration with assigned work steps
- Logistics: Location/provision of semi-finished goods
- Constant key figure evaluation as the basis for CIP
- Recording of energy and consumption data
- Digital provision, for example, of drafts to machine
HAUFF-TECHNIK: Interconnected logistics
Fast delivery times are a central aspect of INDUS subsidiary HAUFF-TECHNIK’s success. HAUFF-TECHNIK manufactures cable and pipe feed-throughs in Hermaringen. This is no easy task – with highly variable production that covers the whole range from individual items to series production. But with the construction of a new 5,500 m2 automated logistics center, which was completed in 2021, 85% of all orders can now be met within 48 hours. The ERP system records and manages up to 4,500 transport moves directly each day. This makes a difference. 90% of the goods go through the fully interconnected logistics center in less than two hours.
These are just three of many examples of how INDUS companies use the opportunities offered by connected IT for success. Who knows what opportunities AI will bring in the future? One thing is certain though: INDUS companies will examine the opportunities and make the most of them if they’re right for them.
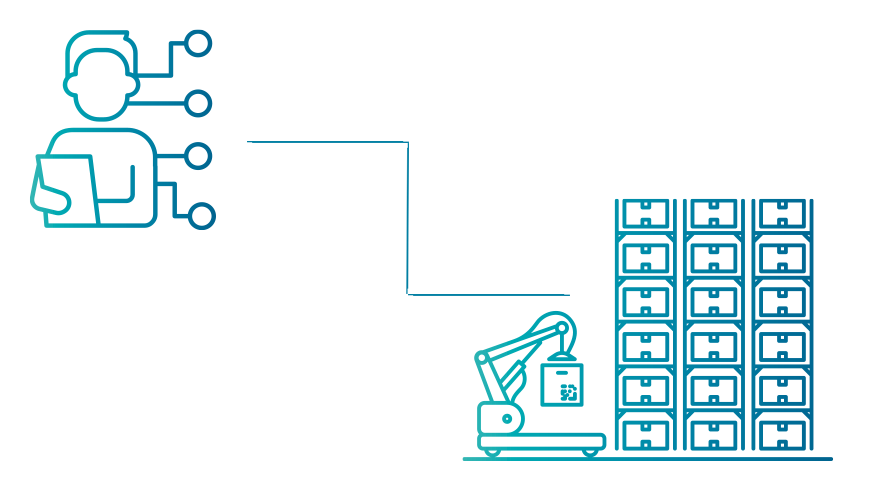
Digital from A to Z: WIRUS Fenster
WIRUS Fenster has been part of the INDUS Group since 2021. A company that has integrated digitalization throughout its value chain. From quotes to order processing, from LEAN manufacturing to logistics, WIRUS’s networked IT system enables orders to be processed quickly and efficiently across systems. And to continually grow in a consolidating market, almost as a side effect.
WIRUS manufactures around 150,000 windows and 11,000 front doors each year. Fully automated, paper-free production allows an efficient implementation of the just-in-time principle. This allows WIRUS products to be produced at the right time and in the right amount. Without an intermediate or finished-goods warehouse. Thanks to a high level of digitalization, one-off production is possible within just a few days. The foundation for this is the connection of the entire supply chain – from the manufacturer to the courier and then to the customer.
In addition to their speed, the Rietberg-Mastholte-based window specialist is also committed to sustainability. All components of WIRUS windows are fully recyclable. Theoretically, the loop of window use and recycling can be completed at least seven times – without any deterioration in the high level of raw material and processing quality.